The pneumatic system of the Airbus A320 plays a crucial role in the aircraft’s operation by providing pressurized air for various functions essential for safe and efficient flight. This system is designed to operate seamlessly with other aircraft systems, contributing to functions such as engine starting, air conditioning, and de-icing. Understanding the components, operation, and significance of the A320 pneumatic system is vital for comprehending its role in modern aviation.
Overview of the Pneumatic System
The pneumatic system in the A320 primarily utilizes compressed air generated by the engines. It harnesses bleed air from the engines and the Auxiliary Power Unit (APU) to perform various tasks throughout the aircraft. The system is vital for maintaining comfort and safety during flight, ensuring that critical systems have the necessary air pressure to function effectively.
The control of the pneumatic system is usually automatic. Bleed-Air Monitoring Computers (BMCs) control the automatic function. The BMCs are installed in the avionics compartment. There is one BMC for each engine. You can also control the system manually. The pushbutton and selector switches on the overhead panel 30VU in the cockpit, control the manual function.
You can monitor the operation of the pneumatic system on the ECAM BLEED SD PAGE. The pushbutton switches on the overhead panel 30VU have no indication when the system operates correctly.
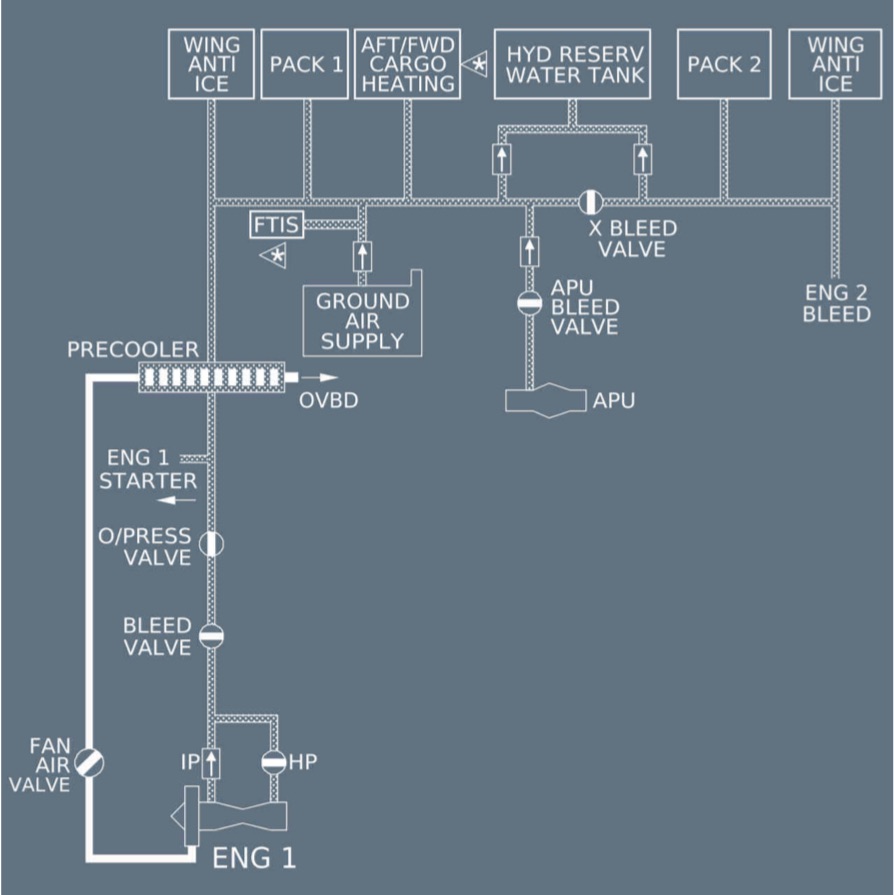
Key Components of the Pneumatic System
Bleed Air System
– The A320’s pneumatic system draws bleed air from the high-pressure compressor section of the engines and the APU. This air is critical for various operations, including starting the engines and supplying air to the environmental control system (ECS).
Air Conditioning Packs
– The aircraft is equipped with two air conditioning packs that condition and distribute air throughout the cabin. These packs utilize bleed air to provide temperature-controlled air, ensuring passenger comfort.
Valves and Ducting
– A series of valves regulate the flow of bleed air. These include:
– Bleed Air Control Valves: Manage the extraction of bleed air from the engines and APU.
– Isolation Valves: Allow for the isolation of bleed air sources if a fault occurs, ensuring system redundancy.
– Ducting routes the pressurized air to various components throughout the aircraft, including the cockpit, cabin, and pneumatic actuators.
Pneumatic Accumulators
– The system may include accumulators that store pressurized air for use during transient demands. These are particularly useful for providing a stable air supply during engine start or when there is a sudden need for high-pressure air.
Ice and Rain Protection Systems
– The pneumatic system is also responsible for providing air to the wing and engine anti-ice systems, preventing ice formation during flight in cold conditions. Additionally, it helps operate windshield wipers and de-icing systems.
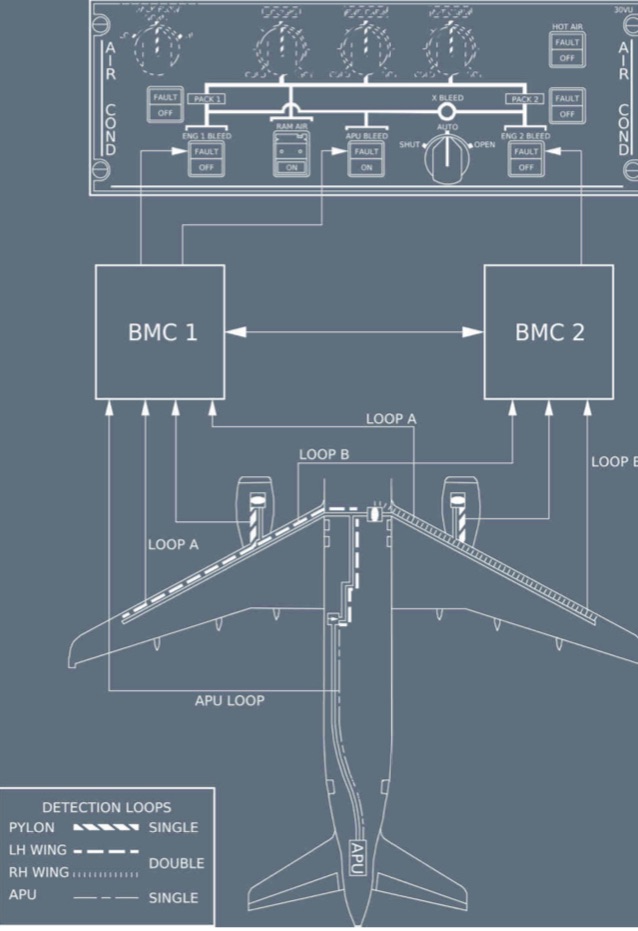
SOURCES
- CFMI engines – Air is bled from the 5th (IP) or 9th stage (HP).
- APU – The air is bled from the APU load compressor.
- The APU can supply bleed air up to an altitude of 20000 ft.
- HP ground connection.
Operation of the Pneumatic System
Engine Start
– During engine start, bleed air is extracted from the APU or the operating engine. This high-pressure air is directed to the engine starter, enabling the engine to start efficiently.

Cabin Pressurization and Air Conditioning
– Once in flight, bleed air from the engines is routed to the air conditioning packs, where it is cooled and conditioned before being distributed into the cabin. The system maintains cabin pressure by continuously monitoring and adjusting the flow of bleed air.
Environmental Control System
– The pneumatic system interacts closely with the ECS to regulate cabin temperature and pressure. Sensors continuously monitor conditions, allowing the system to make real-time adjustments to ensure a comfortable environment for passengers and crew.
Anti-Icing Systems
– The pneumatic system supplies hot bleed air to the leading edges of the wings and engine inlets. This heated air prevents ice accumulation, which can significantly impact aircraft performance and safety.
USERS
- Wing ice protection system
- Air conditioning system
- Engine starting system
- Hydraulic reservoir pressurization system
- Pressurized water system
- Nacelle anti-ice valve (servo pressure)
Safety Features and Redundancies
The A320 pneumatic system is designed with multiple safety features to ensure reliable operation:
Redundancy
– The system includes multiple bleed air sources (from both engines and the APU) and valves that can isolate malfunctioning components. This redundancy ensures that if one source fails, others can take over to maintain necessary pressure.
Monitoring Systems
– The aircraft’s ECAM (Electronic Centralized Aircraft Monitor) system continuously monitors the pneumatic system. It provides real-time data and alerts to the flight crew regarding any irregularities, enabling prompt corrective actions.

Maintenance and Inspection
– Regular maintenance checks and inspections are conducted to ensure the integrity of the pneumatic system. These checks include verifying the operation of valves, ducting integrity, and overall system performance.
Conclusion
The pneumatic system of the Airbus A320 is an essential component that supports numerous critical functions within the aircraft. By efficiently managing pressurized air from the engines and APU, it ensures safe and comfortable flight operations. Understanding the components, operation, and safety features of the pneumatic system underscores its importance in modern aviation, highlighting the sophisticated engineering that underpins aircraft safety and performance. As technology advances, the reliability and efficiency of systems like the A320’s pneumatic system will continue to evolve, further enhancing the safety and comfort of air travel.
For all aviation-related guidance (DGCA ground classes, pilot training, cabin crew training)
Contact us https://contrail.in/
phone numbers +91 78457 69399